December 24, 2023
Understanding the Industry 4.0 Pyramid: A Step-By-Step Guide to Smart Factory Transformation
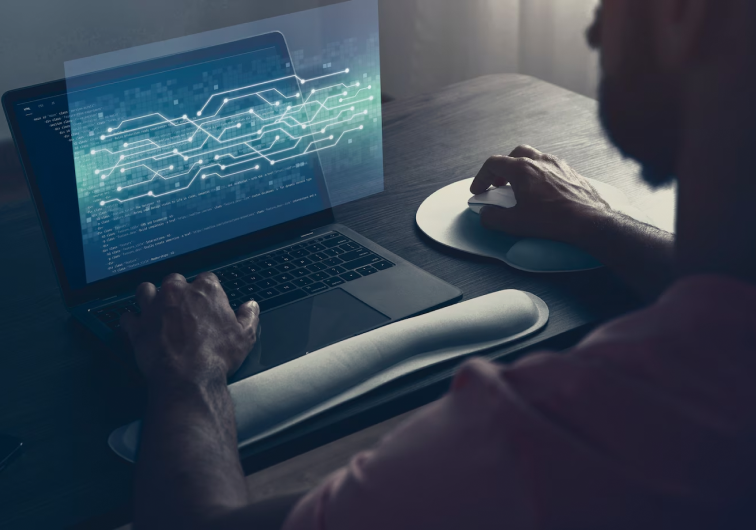
The fourth industrial revolution popularly known as Industry 4.0 is dramatically changing the manufacturing industry and transforming it in an intelligent way. Driven by a slew of advanced technological innovations, Industry 4.0 will redefine how the products are designed, manufactured, and supplied to the end consumers.
Smart manufacturing a leading force behind Industry 4.0 is making machines capable of communicating with each other to make the workflows more optimal and efficient.
Industry 4.0 and Smart manufacturing are two tightly coupled concepts – both employ advanced technology for efficient manufacturing operations – but they aren’t the same. Smart manufacturing is limited to only the manufacturing level while Industry 4.0 is a broader concept and it enables smart manufacturing. Industry 4.0 creates and optimizes inter-connected production ecosystems and revolutionizes the manufacturing industry.
This article entails the five levels of Industry 4.0 and how these levels can enhance manufacturing intelligence and efficiency. So, without further ado, let’s begin by discussing the basics: what is Industry 4.0 Pyramid?
What is the Industry 4.0 Pyramid?
Industry 4.0 or the fourth industrial revolution is the running time of manufacturing and industries which are witnessing rapid transformation. The digital-physical technologies such as the Internet of Things (IoT), Big Data, and Artificial intelligence (AI) are the main driving forces of Industry 4.0. These technologies enable rapid data exchange, advanced analytics, and different levels of automation.
The Industry 4.0 pyramid consists of these different levels of automation which are responsible for the flow of information within a smart factory. There are 5 major levels in this pyramid. These are:
1. Machinery Sensors
2. Control Systems
3. Supervisory Control and Data Acquisition (SCADA) Level
4. Planning Integration
5. Strategic Business Integration – ERP System
We will delve into each of these levels in detail.
Machinery Sensors (Level 0):
At this level, there are sensors that can collect information from all switches, equipment and other input devices and make decisions about what output to deliver to complete the given task.
The most common types of sensors used in Industry 4.0 detect level, electric current, humidity, pressure, temperature, proximity, heat, flow, fluid velocity, and infrared radiation.
Control Systems (Level 1):
There are PLCs (Programmable Logic Controllers) and PIDs (Proportional – Integral – Derivatives) that operate at this level. In PLCs, there is a processor and a memory to manage programming, data, and input/output modules; on the other side, PIDs are integrated into PLCs to maintain a process at a desired setpoint.
The best relative epitome of the machinery sensors usage is the cruise control in cars. In cruise control, the driver can set the desired speed and leave the foot from the accelerators. The set of sensors and the processor in a car will maintain the same speed until any objection by the driver through brakes.
At the industrial level, a heater is a great example. Heaters are required at various operations in industrial plants. The PLC-PID combination helps to attain a desired temperature at a constant level.
Supervisory Control – SCADA Systems (Level 2):
Just like the previous level employs PLCs, this level uses SCADA systems. SCADA refers to supervisory control and data acquisition. It is an amalgamation of previous levels to synthesize data and control systems from a single point. It helps in controlling machines remotely by adding a GUI like HMI (Human Machine Interface). A basic example of HMI is an ATM whose screen and push buttons let you operate the machine to withdraw cash.
What makes SCADA systems important is that they are able to monitor and control multiple systems from a single location.
Planning Integration (Level 3):
The fourth level of the Industry 4.0 pyramid is called Planning Integration. At this level, a computer management system known as MES is employed. MES refers to a manufacturing execution system that can monitor the entire manufacturing process in an industrial plant.
Thus the managers can easily see and check if everything is going as per the defined process. They can also make quick decisions if they encounter any anomalies. It includes adjustment of raw material orders or shipments as per the real-time data generated by systems.
Strategic Business Integration – ERP Systems ( Level 4):
This level uses the integrated management system i.e. ERP of the companies. At this level, the top leadership of the company can oversee the operations and overall performance. ERP is a collective suite of different applications that can oversee everything in the company. It leverages the technologies of all the other levels along with some additional software for such level integration.
This allows top management to monitor and control all business operations of manufacturing, sales, purchasing, finance, payroll, and others. ERP integration brings efficiency and transparency within a company by keeping everyone on the same page.
Data Analytics and Reporting:
There is a predominant role of data analytics and reporting in the Industry 4.0. The data collected through smart sensors are analyzed with technologies such as Big Data, Qlik, Tableau, Tensorflow, etc. These tools are necessary to provide data-driven insights for optimization and decision-making.
The data helps in various manufacturing scenarios such as in batch processing plants, welding lines, assembly lines, machining lines, etc.
FAQs:
1. How do Industry 4.0 technologies reduce manufacturing downtime?
The real-time monitoring of the entire assembly line, machining line, and equipment will provide you with updated insights into any potential maintenance required by any equipment. Thus, the maintenance can be carried out before any major breakdown which ultimately reduces the downtime.
2. What are the initial steps in adopting Industry 4.0 in existing setups?
To adopt Industry 4.0 in the existing setups, the steps are followed just like the levels of the I4 Pyramid. There are sensors integrated at the machine level and the data is collected. This data is further analyzed and a refined view is presented through ERPs to the top management.
Conclusion:
Industry 4.0 is the future of the manufacturing industry. It isn’t just limited to bringing efficiency in the operations, reducing downtime, and ultimately profits but it also brings a better quality of the final products. The Industry 4.0 pyramid components are designed to meet modern industry requirements. At LineCraft, we leverage the latest technologies and craft the best AI solutions to bring automation to your industrial plants. We can increase efficiency, reduce downtime, and bring innovation to your products.