January 7, 2024
Breakthrough in Bottleneck Analysis using Industry 4.0
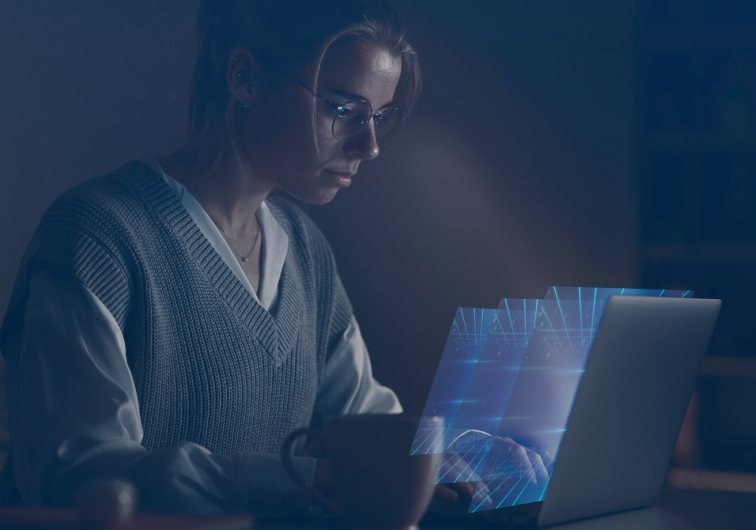
Serial production has become the norm in design of the manufacturing processes in modern times. The serial lines work by serially interlinking machines carrying out different operational steps through part transport (conveyors, robots, trolleys), such that multiple machines are operating on different operating steps of different parts parallelly, to deliver one finished part at the end of the line at a “takt time” that defines production rate of the line. It is a common practice to name the operational steps as OPs, numbered serially in intervals of 10 (like OP10, OP20, etc.) to enable any additional OPs to be inserted in the sequence later-on.
The takt time of any individual operating step is defined by two factors:
- The production rate of various assets involved in completing the step (machines, transport and tools)
- The rate of inputs to that step (operators, sub-parts being added on the line)
The “constraint” (also called the “bottleneck”) in the line is that operating step which takes the maximum time in the serial operations. Both its upstream and downstream neighbours produce faster than this operating step.
This means that the faster upstream processes are blocked, i.e., forced to wait for the bottleneck process to catch up; whereas the downstream processes are starved, i.e., not receiving parts at the rate they could handle. This way, the entire line experiences an “idle time” while bottleneck asset keeps working.
Identifying the Bottleneck is the Key to Optimizing Manufacturing Performance.
The bottleneck, being the slowest step, sets the pace for the entire production line. Hence, improving the efficiency of the bottleneck operation directly enhances the productivity of the entire production line.
Improving the performance of non-bottleneck processes beyond the pace set by the bottleneck will increase the idle time, and not improve the production.
Eli Goldratt’s book, “The Goal” famously made this “Theory of Constraints” approach popular in manufacturing.
When Does an Asset Become a Bottleneck?
Current industrial practices recognize that the bottlenecks may be caused by
- Performance (assets working slower than required rate)
- Availability(assets stopping to work due to failures or “down time”)
- Quality (assets producing bad parts that cannot be processed further by next operations)
Are Pre-designed Bottlenecks a Convenient Solution?
Since it is extremely difficult to manage lines with shifting bottlenecks, line design practices propose a “managed bottleneck” approach – intentionally creating a single bottleneck by design (“design bottleneck”) at or towards the end of the line. At least in theory, this allows only one process to be focused on to be run optimally.
However, this convenience comes at a cost, because it would mean overdesigning all other assets, effectively using them ineffectively. Hence, this approach is rarely practiced.
Furthermore, by design only the performance bottlenecks can be predesigned. The availability & quality bottlenecks are not expected through high reliability and high process capability machines to ensure relatively low impact to cause bottlenecks. Wherever a high impact or risk is anticipated – a “buffer” is designed to store the parts before & after the process step where high variation is expected, and design the process step itself for a higher throughput than the expected line throughput.
Traditional Approach to Identifying the Bottleneck Operation
A measure of line performance, OLE (overall line effectiveness) and individual asset performance, OEE (Overall Equipment Effectiveness) capture these performance measures, allows the manufacturing engineer to evaluate how the line is performing. For a typical manufacturing line, 85% OEE is considered a “gold standard”, while in reality, lines only perform between 60% to 80%.
When the performance of the line is lower than expected, it is required to identify the bottleneck that is causing the performance loss.
If the bottleneck is “persistent” (consistently present with statistically repeatable behaviour), there are Industrial Engineering techniques available for identification:
- Performance bottleneck can be identified using cycle time study, filtering out the waiting times of the asset to compute the net cycle time of the asset.
- Availability / MTBF / MTTR studies will capture downtime bottlenecks.
- FTQ studies can capture quality bottlenecks.
IIOT (Industrial Internet of Things) – One of the pillars of Industry 4.0 – aims to boost the manufacturing performance through use of data. It promises not only to enable Industry to reach the elusive 85% OLE – but to set new standard for industry that will exceed 85%.
In a series of mini bulletins that follow, the principle sand examples of this improvement through use of IIOT – specifically the Linecraft AI product suite, that enable this transformation.
Industrial Engineering Approach has Multilateral (and often Hidden) Challenges
The “managed” bottleneck is no longer supported by the industry, since this makes all the other assets idle, wasting the effectiveness of their investment. As a result, serial manufacturers build “balanced lines”(no design bottleneck) where all the operational steps are designed to perform very close to the required takt time.
In a balanced line, there are “transient” variations in performance - which aren’t systemic issues with the line but instead, short lived disturbances caused by temporary factors. Transient variations or operational variances lead to some mismatches in time-to-time production rate. This makes it very difficult to pinpoint the bottleneck – because each time the performance of the line is monitored, different observations are captured.
What makes the problem significant is that in a serial line, the losses are multiplicative. Any stoppage on the line will cause partial blocking & starving of all other assets. For instance, let’s assume that all assets are operating with 97% OEE, but if their slowdowns and stoppages happen at different times, the OLE of the serial line of a 20-stepprocess will drop down to a meagre 54%.
Multiple such issues happen in multiple assets at multiple times under different conditions. Trying to fix the issues as they are being observed ends up in a “whack a mole” approach – a lot of effort, but no result. If there was a way to identify “top issues” and work on them selectively, this process can become manageable.
Finally, creating buffers to isolate the effects of such losses from serial production have their own limitations – it bloats up work-in-progress causing financial loss, consumes space, causing capital loss, issues remain hidden longer – causing waste, hence directly contradict single piece flow principles.
Therefore, if buffers are to be provided, they should be only a few select locations, and in minimum quantities. These decisions also require analytic tools to be able to identify top priority issues, their causes and controllability (one would correct the controllable issue, rather than buffer for it), and their frequency (to identify optimum quantities).
What causes the “Transient Bottlenecks”?
There are various use cases in practice, which although might happen in 5-10% of the cases of cycles on each asset, their cumulative impact in the line performance can be devastating. Only a few common examples are captured below:
1. Effect of cycle time variance:
90% cycles are happening within cycle time - even faster than cycle time, but 10% of the cycles take slightly longer due to some cycle time elements – like manual actions, readjustment of the part position, part cleaning/verification tasks, replacing defecting part, etc. In this case, the average cycle time may be within required cycle time, but the 10% cycles which exceeded the cycle time led to other assets being blocked and starved for the exceeded time – creating a multiplicative slowdown effect on the production.
2. Effect of acyclic operational requirements:
Some periodic operational requirements periodically (like bin / trolley exchange, calibration verification, tool change, SPC, PM tasks like machine and chip cleaning) cause higher time repeatedly after a few cycles. The machine itself might have its production rate compensated for these losses, but for the line, the faster production rate only results in idle time for the machine, but slower time causes other assets to be blocked or starved.
3. Effect of line operation requirements & constraints:
Practical considerations (like shift changes, setup changes, operator breaks, and material logistics delays) cause loss of cycle time at the boundaries of these actions – and the performance effect cascades in the serial lines until again a “rhythm” of production rate is reestablished.
4. Effect of interactions between assets, flow path disturbances:
Disturbances in the flow path creates transient bottlenecks – including interface conditions, interlocks, and waits between interacting assets like machines & the transport systems, different paths caused by merges & diverts by series parallel path combinations, or rework loops.
5. Effect of micro-interruptions/stoppages:
When a serial production line has multiple unstable processes or assets which cause micro-stoppages, their combined effect on the line flow cascades, causing a significant impact on the line performance.
These issues do not get caught in the conventional asset-based bottleneck analysis because they are transient and might not even have a significant OEE loss at asset level. If one tries to observe and analyse, the cases might be neglected because superficially, they look intermittent and low Impact.
The New Approach to Bottleneck Analysis – using Linecraft AI
Industry 4.0 tools have emerged to help to solve such problems, that were previously thought unsolvable. These tools are based upon analysis of a large volume of data over a large period of time, eliminating the limitations of not having detailed-enough information and not enough time of information.
The most logical solution for identifying bottlenecks is to monitor the “flow”. Structural bottlenecks will case a low flow throughout the line, but transient bottlenecks will cause dynamic increases and decreases in the flow at different sections of the line. Industry 4.0 tools enable this very analysis, providing a direct view into both types of bottlenecks.
Linecraft AI is one such analysis system, that has a unique algorithm which is able to distinguish the times attributable to assets own operation, and the time loss caused by the effects of “external” factors – not intrinsically a part of the asset operation .This enables the “flow” through the assets to be modelled by “waits” caused in the asset, and form patterns over larger periods of analysis for:
- Structural bottlenecks (Specific assets are always bottlenecks – this might be due to the asset’s own issues like high cycle times, or low availability)
- Transient bottlenecks (Specific assets or cells become bottlenecks intermittently)
The transient bottlenecks are then prioritized by impact & frequency to determine opportunities for improvement.
Structural bottlenecks can be eliminated through asset level optimization of the issues – whether due to cycle time by optimization, or availability by pareto analysis of losses, and elimination of the root causes of the specific reliability issues.
For Transient bottlenecks, the main causes need to be identified. Linecraft analysis allows high impact and high frequency issues causing transient bottlenecks to be identified. Once identified, the improvement approaches can then be:
- Improved operating patterns – preparation, planning and setup improvements for the shift, setup, material changes, etc.
- Improvement of equipment/interface design to remove losses in interactions/flow disturbances.
- Buffering the cells with adding buffers to isolate effects of acyclic operations / beyond solution instability issues.